Virtual engineering
Optimal flow
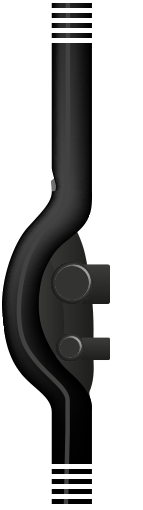
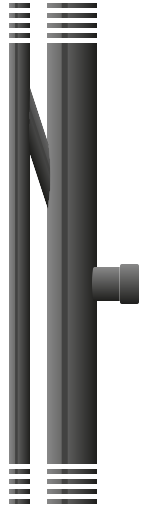
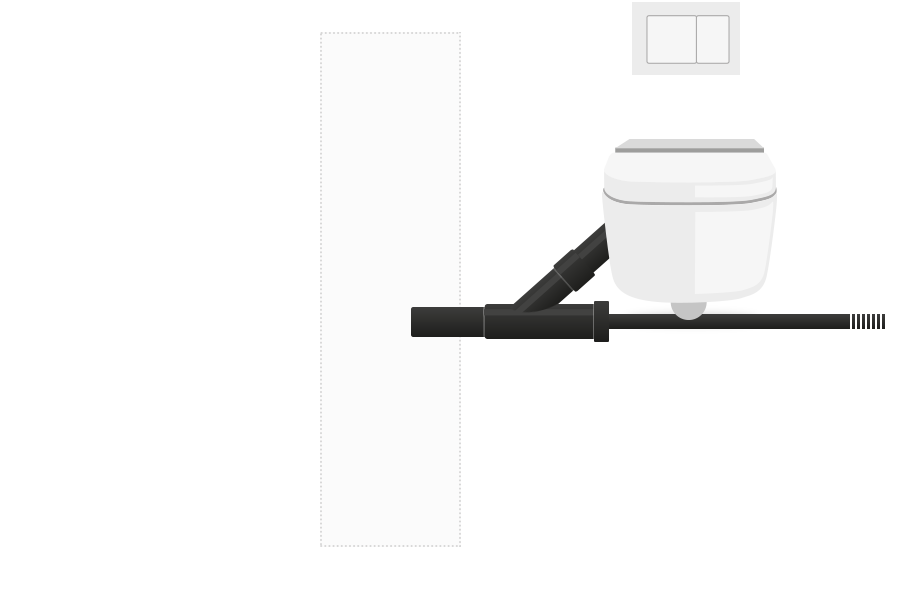

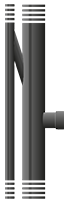
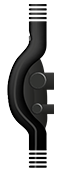
Pushing the limits of what is possible
All drainage systems from Geberit are noted for their excellent flow behaviour.
This is in no small part down to the great work carried out by the flow specialists – the experts
who optimise virtual products on their high-performance computers until the correct performance
profiles are achieved.
Geberit uses computer simulations to determine and optimise the flow behaviour of sanitary components,
long before the first prototypes are made.
Doing so enables time and money to be saved during product development while also allowing solution
approaches to be pursued that would be virtually unthinkable without virtual engineering.
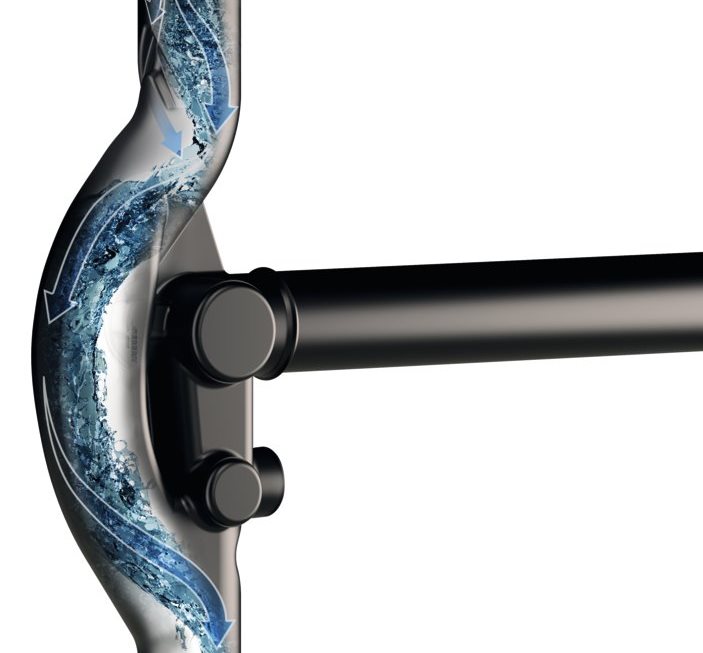
An old trick
This can be illustrated in greater detail using the Geberit Sovent fitting as an example. This fitting is used in high-rises to connect the discharge pipes from an individual floor to the discharge stack. As part of the product optimisation process, the aim was to increase the product’s discharge rate. The key questions here were: What is the highest possible flow rate in theory and to what extent can this value also be achieved in practice? An everyday trick put the flow specialists on the right track. If you want to empty a full water bottle as quickly as possible, you hold it with the opening facing downwards and rotate it gently. This makes the water swirl, enabling an air column to form in the middle of the opening. This air column ensures pressure compensation, which enables the water to drain out of the bottle at a much faster rate.
Major improvement in performance
Inspired by this physical phenomenon, the engineers set to work at their computers and added an asymmetrical kink in the upper section of the virtual Sovent fitting. This caused the – also virtual – water flowing down to rotate just like the engineers had envisaged, creating a continuous column of air in the centre. Initial calculations showed that this design modification had significantly accelerated the flow rate of the water.
After the completion of the simulation work on the computer, the first prototypes were made and tested under realistic conditions in the 24-metre-high waste water tower. The results were clear: Installing Sovent fittings that had been optimised from a fluid dynamics perspective increased the discharge capacity of a discharge stack by 40 per cent.