
Business report > Business and financial review
Sustainability
Sustainable thinking and action as part of the Geberit culture
A sustainable corporate culture makes it possible to increase the value of the company over the long term and minimize risks for its future development. Geberit aims to be a role model and to set standards for customers, suppliers and other partners. This applies to water-saving, sustainable products; environmentally friendly and resource-efficient production; procurement and logistics with high environmental and ethical standards; and good, safe working conditions for the more than 6,000 committed and qualified employees worldwide. The corporate social responsibility is realized among other things within the scope of global social projects relating to the core competence of water and is intensified through partnerships such as that with Swiss WaterKiosk aimed at cleaning polluted drinking water in Bangladesh. There is also a long-term partnership with the Swiss development organization Helvetas.
The 50th birthday of the Geberit concealed cistern is a perfect example of how long-term business success is compatible with environmentally friendly action. This highly successful product, which has been sold over 60 million times, was a far-sighted strategic step on the journey from a sanitary unit to the bathroom of today in its modern form. Water saving through reduced flush volumes, reliable quality and comfort for end users as well as the 25-year guaranteed spare parts availability for plumbers are all convincing aspects of a sustainable product.
Responsible handling of water
With its Millennium Development Goals from the year 2000, the United Nations aims to halve the number of people without access to clean drinking water and sanitary facilities by 2015. This demonstrates the great importance of the topic of water for world health, world nutrition and peacekeeping. The increase in the world’s population, migration, urbanization, climate change and natural disasters can lead to regions that are currently well supplied with water becoming problem regions in the future. These global trends will have a significant impact on future sanitary technology: Water-saving and resource-efficient products are becoming even more important. The EU is increasingly putting water conservation on its political agenda and is developing ecolabels for efficient toilets, urinals, washbasins and showers. As an industry leader in the area of sustainability, Geberit imposes stricter standards on its products than those prescribed by the European ecolabels. In the → product classification system WELL (Water Efficiency Label) for water-saving and resource-saving products introduced by the industry in 2011, seven Geberit product groups are already represented in the highest classification class A.
The continuous reduction of the ecological footprint of Geberit products goes beyond water saving. The → eco-design approach has been implemented since 2007. This means that concepts are tested in their entirety during a product’s early development phase in order to examine how water, energy and material consumption can be optimized. At the same time, production processes are often also simplified and cost savings made. Thanks to this pioneering work on the topic of eco-design, Geberit is well equipped in terms of possible requirements as envisaged as part of an EU ecodesign directive. The ability to think ahead and quickly implement measures in development can also be seen in the handling of the European Drinking Water Directive 98/93/EC, which is valid as of December 1, 2013 and defines a maximum allowable lead concentration in drinking water. All affected components made of copper materials – some 1,800 products – were adapted to the new requirements ahead of time.
System provider of solutions in green building
Green building has long been more than just a trend. European standards in this area are becoming increasingly significant and new standards are setting out the basic rules for → environmental declarations for individual products and systems for buildings, for example. At the same time, more and more buildings are being constructed in accordance with voluntary sustainability standards such as DGNB, Minergie, BREEAM and LEED. Investors, project developers, owners and tenants are looking for system providers with holistic expertise regarding green building that can contribute to the respective desired standards being fulfilled in a targeted manner. This is opening up a future market with major potential in which Geberit is present and well positioned with water-saving, energy-saving, low-noise and durable products. The importance of the topic is also reflected in the increasing number of green building reference projects in which Geberit products are installed. The impressive shopping center → “Emporia” in Malmö sets itself apart thanks to its striking architecture and is also a BREEAM-certified green building. The Mepla piping system and the Duofix installation systems from Geberit meet the stringent BREEAM requirements here. When constructing Shanghai Tower, the world’s second tallest building, those responsible for the project opted for the Geberit Pluvia roof drainage System, which efficiently collects rainwater, enabling over 40% to be reused. Geberit Sigma concealed cisterns and PE piping systems are an integral part of green buildings in Milan’s new skyline: → UniCredit Tower and Bosco Verticale are both nominated for LEED Gold certification.
Sustainability strategy and reporting as a foundation
Geberit’s positioning as a sustainable company is playing an increasingly important role in various stakeholder groups’ expectations, as is reflected by a large number of awards. The consistent implementation of the sustainability strategy is an essential guideline for the development of all internal organizational units. The strategy focuses on individual sustainability modules. Among these are → green procurement, → green logistics, → environmental management in production, → occupational safety and → eco-design in product development as well as → social engagement. Each module contains a clear objective, derived measures and quantified key figures for effective monitoring. Overall, objectives were achieved to a great extent in 2013. For more information, see the → sustainability strategy.
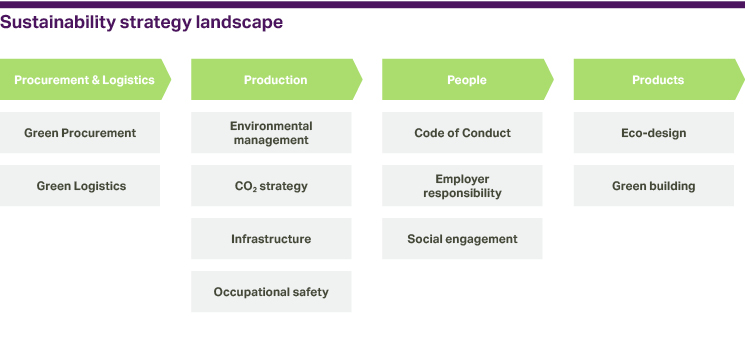
Geberit is committed to internationally recognized principles of sustainability and since 2008 has been a member of the United Nations Global Compact, a global agreement between businesses and the UN designed to make globalization more socially responsible and environmentally friendly. The → Communication on Progress regarding measures in the areas of human rights, labor practices, environmental protection and combating corruption is submitted annually. Geberit is also a member of the local Swiss network of the UN Global Compact. The formal anchoring of the subject of sustainability is reinforced by the → Code of Conduct for Employees and the → Code of Conduct for Suppliers. Compliance with the directives is ensured by continuously improved → compliance processes. In addition, an extensive system for the control and management of all risks involved in entrepreneurial activities is in place throughout the Group. For more information, see → Corporate Governance, 3. Board of Directors, Information and Control Instruments vis-à-vis the Group Executive Board.
A sustainability performance review is published annually in accordance with the guidelines of the Global Reporting Initiative (GRI). All aspects of the guidelines can be found in the → Sustainability Performance Report for 2013. As part of sustainability reporting for 2012, an external stakeholder panel was initiated and consulted for the first time. Its mandate consisted of providing feedback on the company’s sustainability strategy and reporting, as well as reviewing whether the key topics were included in the sustainability reporting and whether the needs of the stakeholder groups were taken into consideration. The results are summarized in a → panel statement. These served as a basis for the further development of the sustainability strategy and reporting for 2013. The next stakeholder panel consultation is due to be carried out in 2014, where key sustainability topics shall also be identified. Focusing on the key issues in the respective company in the reporting is an essential part of the new GRI G4 guidelines published in summer 2013.
The information disclosed within the scope of this report fulfills the maximum transparency grade A set out in the currently applicable GRI G3 guidelines, as has been verified and confirmed by GRI (see → GRI Statement). The presentation of the Econ Award for corporate communication in Berlin demonstrates that the efforts being taken to create more transparent communication on the topic of sustainability are being recognized by others. The integrated sustainability reporting for 2012 received excellent feedback and the silver medal in the Online Reporting category.
The efforts in terms of sustainable business management are also being rewarded by the capital market. At the end of 2013, more than 10% of Geberit stock was held by sustainability-conscious investors. Geberit is strongly represented in the sustainability stock indices and sustainability funds segment. For example, the Geberit share is represented in the Dow Jones Sustainability Index (DJSI) and part of the STOXX Europe Sustainability Index as well as the FTSE4Good Index (Europe/Global), where it is among the supersector leaders in Construction & Materials. In addition, renowned sustainability funds hold the shares in their portfolios. Geberit’s objective is to continue to play a significant role in the future in the “Sustainability” and “Water” investment segments that are still gaining in importance.
Saving water with Geberit products
Thanks to industry-leading research and development, Geberit products impress with their high environmental compatibility and recyclability. The company’s greatest environmental achievement, however, is a result of its contribution to the sustainable use of water resources. The analysis of the entire value chain in the form of a water footprint shows that nearly 100% of the water consumption is attributable to the product usage phase. The savings are impressive: According to one model calculation, the entire dual-flush and flush-stop “fleet of cisterns” produced since 1998 has so far saved around 15,800 million cubic meters of water in comparison with traditional flushing systems. In 2013 alone, the water saved amounted to around 2,000 million cubic meters. This is more than half of the annual consumption of all German households.
Water footprint throughout the value chain (2013)
Provision of
raw materials
is required in the manufacture
of raw materials for Geberit
products.

Manufacturing
used in the manufacturing of
products at Geberit in 2013.

Use
by far occurs during the use of
Geberit products manufactured
in 2013 during their entire service
life (cisterns, urinal flushing
systems and lavatory taps).

Disposal
water is used for the disposal of
Geberit products.

Sustainable products thanks to eco-design
The basis for sustainable products is a systematic innovation and development process in which the most environmentally friendly materials possible are chosen, risks are minimized along the value chain and a high level of resource efficiency is targeted in the area of product design. Eco-design workshops, in which different disciplines cooperate and ensure that every new product outperforms its predecessor in environmental aspects, have been an integral part of product development since 2007. For example, thanks to innovative flow technology, the discharge rate of → Sovent fittings – a product which facilitates an optimal layout of waste water discharge stacks in high-rises – was increased by 40%. Since 2010, eco-design has also been included in product modifications and technology projects, thus ensuring that opportunities to reduce the ecological footprint are always utilized to their full potential.
Specially created product life cycle assessments are important decision-making aids for the development processes and provide arguments for the use of products that conserve resources. Detailed life cycle assessments have already been prepared for the following products: drainage/supply pipes, AquaClean 8000plus, electronic lavatory taps type 185/186, concealed cisterns and urinal flush controls. An Environmental Product Declaration (EPD) was issued in accordance with the new European standard EN 15804 for the first time in 2012. The EPD for lavatory taps provides relevant, comparable and verified information about the product’s environmental performance. New ways of more efficiently creating product life cycle assessments and EPDs for other products are currently being sought. A pilot project for the systematic recording of environmental data at the product level was therefore started, which should greatly simplify a further processing to EPDs and ecological product information.
WELL label documents leading position in the area of water conservation
In 2013, the European Commission formally agreed upon the criteria for an ecolabel aimed at reducing water consumption in European toilets. This label will be awarded to toilets that – in addition to fulfilling other requirements – use a maximum of five liters per toilet flush and therefore contribute to significantly reducing the average water consumption per toilet flush. An industry solution that was introduced in 2011 and supported by Geberit already provides incentives for exceeding these requirements. The WELL label (Water Efficiency Label) introduced by the European umbrella organization for faucet manufacturers (EUnited) takes its direction from the well-known and well-established energy labels for electrical household appliances and serves as an information and orientation aid. WELL provides consumers with information about a product’s water efficiency at a glance. WELL uses a scale of A to D for products for home use and A to F for products for use in public areas. For example, WC flushing systems achieve the A class only if they use a maximum of between four and five liters per flush. As such, these requirements are more stringent than those for the EU Ecolabel. Of the eight Geberit product groups already certified, seven are represented in the A class and one in the B class. These product groups account for around 20% of Group sales. This water-efficiency label has been added to packaging and specified in the catalogs since 2013. The list of products certified in the A class also includes one of the most important products in the Geberit range, the Sigma concealed cistern.
Production with high resource efficiency
All production sites – with the exception of the Indian site, which commenced operations only in the second half of 2013 – and logistics as a whole are subject to systematic, Group-wide environmental management and certified in accordance with → ISO 9001 and ISO 14001. Certification for the entire Group was renewed in 2012 and is valid until 2015. A comprehensive corporate eco-balance is prepared each year as the basis for targeted measures to improve environmental performance. In 2013, the roll-out of the integrated management system for quality, environment, energy and safety was continued at all plants. This includes the further implementation of the software program launched in 2012 for the Group-wide monitoring of the corporate eco-balance, the energy master plan and occupational safety. Among other things, this enables the energy balance to be checked on a monthly basis.
Although currency-adjusted Group sales rose by 3.6% in the reporting year (previous year +4.5%), the absolute environmental impact over the same period declined by 2.1% (previous year -5.1%). The consumption of energy in the form of electricity, combustibles and fuels represents the greatest environmental impact. The consumption of electricity fell in 2013 (111.7 GWh; previous year 113.4 GWh). In terms of combustibles, while the company consumed slightly more natural gas (39.9 GWh compared to 38.1 GWh in the previous year), it consumed considerably less heating oil (0.16 GWh compared to 0.24 GWh in the previous year). Fuel consumption increased slightly (18.2 GWh compared to 17.9 GWh in the previous year). The procurement of green electricity (21 GWh compared to 20 GWh in the previous year) and the use of 10.6 GWh of biogas (previous year 9.4 GWh) reduced the environmental impact and CO2 emissions.
Numerous technical measures have helped increase energy efficiency. For example, the number of injection molding machines retrofitted with energy-efficient drive technology was increased in the reporting year as planned from 74 to 96, with the two Chinese production plants in Shanghai and Daishan benefiting particularly from this development. An analysis on site showed that a modified machine consumed an average of over 40% less energy. This measure enables the Chinese plants to save approximately 2 GWh of electricity per year, which corresponds to over 20% of total electricity consumption. At the site in Pfullendorf (DE), replacing an old blow molding machine with the latest machine technology and using the waste heat from the block heating station contributed to a reduction in energy consumption of around 1.2 GWh per year. The conducting of pre-audits at three German plants for the purpose of implementing the new ISO 50001 standard is further evidence of active energy management.
CO2 emissions in 2013 amounted to 69,909 metric tons (previous year 71,853 metric tons). The ratio of CO2 emissions to currency-adjusted sales was reduced by 6.1% (previous year -10.6%). This enabled the targets set out in the long-term → CO2-strategy to be met. The growing use of renewable energies plays a significant role here. In 2013, the consumption of additionally purchased green electricity amounted to 21 GWh (previous year 20 GWh). Renewable energy sources accounted for 31% of total electricity consumption (previous year 30%). This figure is to be increased to 60% by 2020. The amount of green electricity supplied to the largest production site in Pfullendorf (DE) was increased by an additional 2 GWh to 14 GWh. The Daishan site in China used around 2 GWh of wind power, which corresponds to approximately 60% of the plant’s total energy consumption. At the plant in Givisiez (CH), a roof area of 3,050 m2 was made available for the installation of solar panels. The photovoltaic system produces just under 0.5 GWh of electricity per year, which is equivalent to the amount of electricity consumed by two production lines at the plant. The share of renewable energies in combustibles is also to be gradually increased Group-wide, rising to 25% by 2020. The block heating station in Pfullendorf (DE), which was commissioned in 2012, is fed with 10.6 GWh of regionally generated biogas.
Binding requirements for new vehicles help increase energy efficiency and reduce CO2 emissions. Furthermore, CO2 emissions caused by air travel amounted to 829 metric tons in the reporting year (previous year 769 metric tons). All the corresponding targets and measures are disclosed in detail as part of the company’s participation in the Carbon Disclosure Project (CDP). Successes were also achieved with respect to other environmental factors. Internal water consumption is at a very low level thanks to the exploitation of far-reaching savings potential. Targeted improvements contribute to the diligent handling of water: Examples include the reuse of water in laboratories and the optimization of fresh water test runs in development. Altogether, 131,938 cubic meters of water were consumed in the reporting year (previous year 136,669 cubic meters). The total amount of waste disposed of came to 12,118 metric tons (previous year 11,460 metric tons), with 84% (previous year 84%) sent to external recycling processes.
Geberit is investing in the infrastructure of tomorrow through the holistic planning and realization of new buildings and expansion projects. The use of rainwater, external shading and enhanced ventilation and cooling were implemented at the new production plant in India, which commenced operations in August 2013. Efficiency potentials are also being exploited as part of the expansion of the plant in Villadose (IT). By relocating the warehouses, the 12,000 m2 area can be managed more efficiently in future and deadhead trips can be reduced to a minimum. The factory premises currently being built in → Ruše (Sl) are already serving as a model for green production throughout Slovenia. The site’s holistic energy concept includes the use of all waste heat from industrial processes as well as the complete absence of fossil fuels. The available ground water is used for cooling, while rainwater is collected and used both as fire fighting water and for watering the surrounding area.