Dear shareholders,
As is the case every year, we would like to mark the publication of the annual report by examining one of Geberit’s special skills in more detail. This time around, we are focusing on our investing activities. In 2018, investments in property, plant and equipment and intangible assets reached a new all-time high of CHF 162 million. The largest part of this sum was used for expanding and modernising our production capacities and for the permanent optimisation of processes. What is probably unique – at least in the sanitary industry – is the systematic way in which investment projects of all sizes are approached.
We would like to take this opportunity to introduce this way of thinking and, using four current examples, demonstrate how we put investment plans into action.
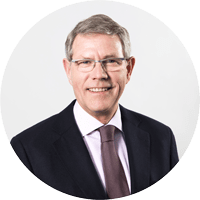
Chairman of the Board of Directors